overview
Semiconductor manufacturing factories, nanotechnology centers, nanofactories, and other precision manufacturing and research centers typically combine cleanrooms with active false floor systems to meet complex facility requirements (pipelines, cables, gas pipelines, etc.) and maintain strict cleaning standards. This type of ground is not suitable for production, testing, and measuring equipment that is sensitive to vibration. The activity ground cannot provide the necessary quiet vibration environment for these tools. TMC's Quiet Island provides an innovative solution by replacing a portion of the active ground area with a "Quiet Island" fixed on the ground floor below. Quiet Island includes a cleanroom compatible platform top and an application and site specific support structure.

Vibration attenuation
The main supporting components and core technologies of Quiet Island are integrated into the STACIS III active vibration damping system. This "rigid" inertial vibration damping support system is an ideal choice for any vibration sensitive instrument, enabling such tools to operate at high standards in noisy environments. STACIS III is compatible with automated wafer processing tools, high-resolution electron beam imaging tools, ion beam milling tools, and any tool with passive or active internal isolation systems (please refer to our white paper on stacking active isolators on top of active isolators). In addition, it also provides isolation performance over a wide frequency range. And the 'hard installation' design is very sturdy, so there will be no stability issues for higher, heavier tools.
Riser and bracket
The extremely sturdy and durable riser used to support the STACIS isolator is designed by TMC's experienced engineering team and manufactured by our ISO 9001 factory according to high standards and welding certification specifications. Each Quiet Island is carefully designed to accommodate various activity ground heights, underlying ground geometries, and tool sizes. TMC has installed thousands of devices worldwide that support over 200 different instrument models, possessing extensive knowledge and experience to design support structures that meet the needs of STACIS and your facility.
Rigid platform
The platform consists of a 4-inch (100mm) thick steel plate sandwich designed and manufactured by TMC, with the steel plate sandwiched around a lightweight, incompressible, and damping core material. The layered effect of bonding rigid steel plates and cores with epoxy resin to a seamless stainless steel disc provides extremely high stiffness and structural damping. The large cross-section and steel content result in a very high overall stiffness. The top and sides are a continuous integrated stainless steel shell to maintain cleanliness, aesthetics, and integrity. TMC can design and manufacture application specific platforms as needed, including cutouts, special shapes, fixing holes, and eyebolts.
Quiet Islands vs. Quiet Buildings
Designing a facility to meet the stringent Vibration Criteria of extremely precise imaging equipment can be very challenging, and often cost-prohibitive, particularly when not all tools in the facility require these very low vibration levels.[1]
Statistical representation (in terms of Mean plus Sigma Spectra) of vertical vibrations in a typical semiconductor fab production area at 'as built' and two times thereafter [2]
It is very difficult to isolate very large areas such as entire buildings, or an entire floor. It is also well documented that building vibration levels will increase relative to a design specification as the facility is populated with equipment and people. Repeated vibration measurements a few months, or a year later, show that floor vibration levels typically rise over time.[2]
The more cost effective and successful approach for achieving the stringent requirements of vibration sensitive tools, is to employ point-of use active vibration control with serial piezoelectric technology, particularly to mitigate challenging low frequency (less than 5 Hz) vibration (example here).
TMC can work with the your team to design a tool-specific Quiet Island solution. This process allows us to look at each tool specifically and provide the best performing solution. A building design incorporating one large concrete sub-floor “slab” with a “raised floor” allows for flexibility of tool selection post-construction. Replacing the raised floor with a Quiet Island only where needed provides the most sensitive tool set with a vibration environment an order of magnitude, at least, lower than the sub-floor.
See also The Benefits of Including Floor Vibration Control for Nano-Tech Facilities over Designing 'Quiet' Buildings article on AZO Nano.
1Evolving criteria for research facilities: I – Vibration, Colin Gordon Associates, SPIE Conference 5933: Buildings for Nanoscale Research and Beyond, 2005, Source
2Maturation of the Vibration Environment in Advanced Technology Facilities, Colin Gordon Associates, Journal of the IEST, V. 48, No. 1, 2005, Source
Advantages of Quiet Island
Adopting the active piezoelectric vibration damping technology, "hard installation" design, and tool compatibility with built-in isolators starting from 0.6 Hz, which is the industry's leading technology in the field of STACIS-TMC.
Flexibility in modularity, customization, and repositioning - Each platform is tailored to the customer's application, but unlike concrete platforms, these platforms can be easily reconfigured if there are changes in tools or ground characteristics.
Professional knowledge - TMC has extensive experience in collaborating with semiconductor manufacturers, research institutions, and ultra precision OEMs. We understand our customers and their needs. We design and manufacture it ourselves.
performance

On a 24 inch high, 40 inch x 60 inch Quiet Island with 4 STACIS stands
Measurement of Transmittance under VC-C Input from the Ground
specifications
Performance specifications
Active degrees of freedom | 6 |
Active bandwidth | 0.6 Hz - 150 Hz |
Passive natural frequency | 18 Hz vertical and horizontal |
Effective active resonance frequency | 0.5 Hz |
Isolation at 1 Hz | 40% - 70% |
Isolation at ≥ 2 Hz | ≥90% |
Stability time after 10 pounds (4.5 kilograms) step input (reduced by 10:1) | 0.3 seconds |
internal noise | <0.1 nm RMSd> |
The working load range of each isolator | Low load capacity: 400-1100 pounds (181-499 kilograms) Medium load-bearing capacity: 900-2100 pounds (408-953 kilograms) High load-bearing capacity: 1900-4500 pounds (862-2041 kilograms) |
Stiffness (1000 pounds/454 kilograms mass, medium load-bearing capacity isolator) | 40000 pounds per inch (73 x 10)5Cow/meter |
Magnetic field emitted from a distance of 4 inches (102 millimeters) from the isolator | <0.02 μG broadband RMSd> |
Design, size, environmental and utility requirements for isolators
Environment and safety | Compliant with CE and RoHS standards |
Active isolation component | **A piezoelectric actuator with a small load-bearing capacity of 3300 pounds (1500 kilograms) receives signals from a high-voltage amplifier and outputs up to 800 VDC. The effective load of vertical actuator supporting vibration isolation |
Passive isolation element | Single hard isotropic elastomer (without compressed air source) |
Vibration sensor components | Downward seismic detector type inertial sensor, used to measure ground vibration below the isolator and provide voltage proportional to the speed of vibration motion |
Active feedback control loop | Measure, process, and attenuate ground vibrations beneath springs supporting isolation surfaces |
Dimensions of isolator (width x depth x height) | 11.75 x 12.5 x 10.8 inches 300 x 320 x 275 millimeters |
Weight of isolator | 75 pounds (34 kilograms) |
operation temperature | 50° - 90° F 10° - 32° C |
storage temperature | -40° - 130° F -40° - 55° C |
humidity | 30 - 60% |
System power requirements | 100、120、230、240 VAC 50/60 Hz AC; <600 W Compliant with CE standards |
ground displacement | <480μin. (12μm) below 10Hzd> |
Number of isolators for each system | At least 3 |
Optional Accessories | Laminated stainless steel platform, frame, riser, leveling device, seismic device, lifting cover |
DC-2020 Controller Specifications
Dimensions (width x depth x height) | 19 x 8.5 x 1.75 inches 483 x 216 x 45 mm |
weight | 6.3 pounds (2.9 kilograms) |
processor | 150/75 MHz dual core |
sampling rate | 10 kHz |
Analog Output | 16 channels |
analog input | 16 channels |
STATUS | Single LED |
Front panel port | 1 serial USB 2.0 1 serial Micro USB 1 Ethernet RJ-45 2 BNCs |
Rear panel port | 1 serial USB 2.0 1 Ethernet RJ-45 1 RS-232 DB-9 traditional serial for traditional STACIS 2100 isolators |
user interface | Front panel LCD display screen Character menu on the super terminal Extended GUI for Microsoft Windows Embedded Ethernet GUI |
Other
Platform surface | Top and side surfaces of stainless steel; Epoxy painted steel bottom |
platform structure | Exclusive multi-layer laminated steel plate |
size | mtm |
standard | 15. 18, 20, 24, 30, 36, 48 inches 38, 46, 51, 61, 76, 91, 122 centimeters Customized height can also be provided |
Load capacity | mtm |
Rigid riser and bracket | Certified welding and all steel structures, Powder coated surfaces compatible with cleanrooms |
Optional Accessories | Limiting brackets, platform top lifting ring bolts, Bridge deck for grid style bottom floor |
Top version of the platform | Cut, through-hole, threaded hole for fixing tools |
otherQuiet Island configuration
Large instruments without environmental vibration specifications typically require a rigid and stable support separate from the active ground. Rigid Quiet Island is the ideal solution. The rigid Quiet Island has the same high-performance platform top, and can also be customized for any height, any bottom floor geometry, and various tool sizes for mobile floor cleanrooms. TMC offers a range of different types of pillars to meet various needs, resulting in modular, flexible, and upgradable solutions specific to instruments and factories.
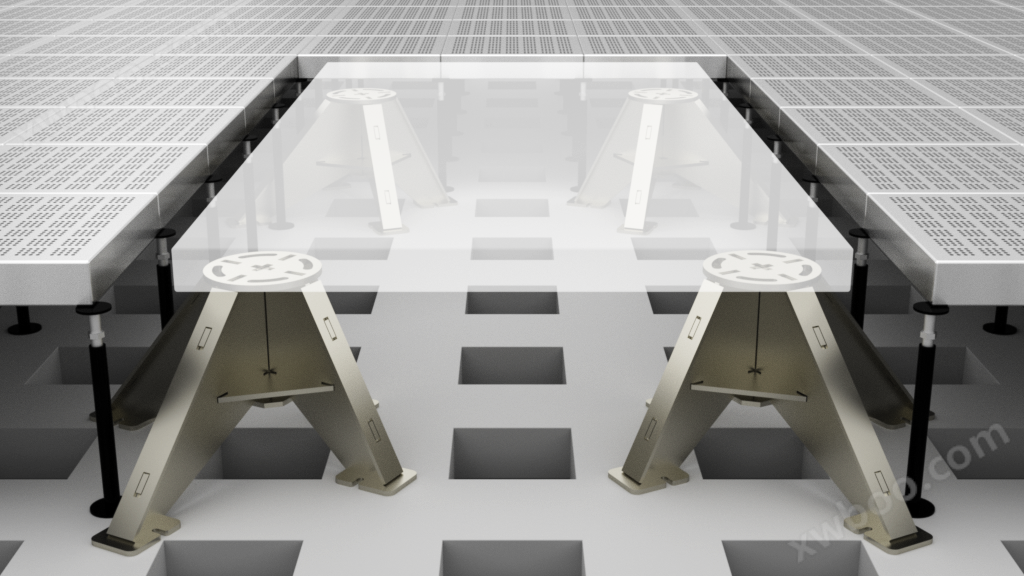

Apply photos





Due to installation on our Quiet Island ® We have not created a standard catalog for ordering the complexity, sensitivity, and value of equipment on the underlying ground platformnumber.
We believe that each platform should be custom designed for specific applications. The recommended ordering steps are as follows:
▪ Tell us the equipment or instrument you want to isolate. Due to the installation of thousands of devices, we may already have a platform design that meets your application requirements. In addition, we maintain close contact with manufacturers of stepper, aligner, SEM, and other tools, so we are aware of new size, shape, weight changes, and ground vibration specifications.
▪ Alternatively, you may want a platform suitable for active ground grid systems. Customers typically choose a platform measuring 47 x 47 inches (1190 x 1190 millimeters) to replace even numbered tiles.
▪ Tell us the height of your activity ground above the solid underlying ground.
▪ Please describe or provide us with an illustration showing any hole patterns in your ground floor or steel beam/grid plate geometry.
▪ Please provide us with ground vibration data or discuss with us how to arrange the measurement of these data.
▪ Consider the vibration sensitivity of the instrument. Our rigid, non resonant pillar design provides ample support for many tools. More sensitive applications will require air or piezoelectric support